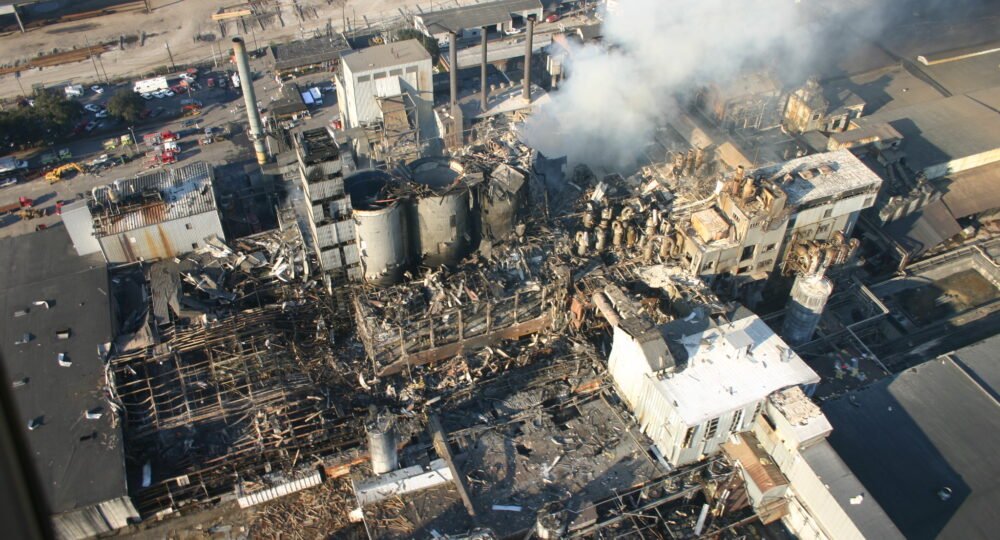
Lições Explosivas | O Caso Imperial Sugar
É irônico pensar que uma empresa dedicada a produzir um dos ingredientes mais doces do nosso cotidiano deixou lembranças tão amargas na história da segurança industrial. Em uma noite de fevereiro de 2008, a fábrica da Imperial Sugar em Port Wentworth, Geórgia, foi palco de uma tragédia que resultou na morte de 14 trabalhadores e feriu dezenas de outros, 14 deles passando meses no Centro de Queimados Joseph M. Still. Por ter ocorrido durante à noite, este evento resultou em fatídicas 14 mortes – um número que poderia ter sido muito maior se tivesse ocorrido durante o dia. Este desastre, causado por explosões de poeira de açúcar, serve como uma lição sobre os perigos ocultos nas indústrias de processamento de alimentos.
O Acidente
O açúcar granulado, um produto aparentemente inofensivo, acumulava-se na saída do silo principal da fábrica. Os operadores frequentemente encontravam torrões de açúcar bloqueando os dutos de descarga, um problema recorrente que exigia intervenção manual. Utilizando barras de aço, eles quebravam os torrões para liberar o fluxo, um procedimento que, sem o conhecimento dos trabalhadores, contribuía para a dispersão de pó de açúcar no ambiente confinado do transportador de correia.
Para agravar a situação, esporadicamente, o canal do silo que despejava o açúcar na esteira entupia, e uma grande quantidade de produto era jogada no chão. Para evitar o desperdício, toda a esteira foi fechada com painéis de aço. Essa medida criou um local sem ventilação, aumentando o risco de formação de uma nuvem de poeira explosiva. Além disso, o fechamento da esteira impedia a identificação de possíveis obstruções dos silos ou problemas de funcionamento da esteira.
As máquinas eram conectadas a um sistema de coleta de pó, mal dimensionado e em mau estado. Esse sistema ineficaz não conseguia lidar com a quantidade de pó gerado, permitindo que mais poeira se acumulasse e se dispersasse no ambiente. A combinação dessas falhas criou um cenário propício para um desastre iminente, onde a mínima faísca poderia desencadear uma explosão devastadora.
A Primeira Explosão
A ignição primária ocorreu devido a um mancal de rolamento superaquecido dentro da transportadora de correia. Funcionários relataram posteriormente que às vezes os rolamentos funcionavam mal, e superaqueciam. O calor desses rolamentos, combinado com a alta concentração de pó de açúcar, criou uma reação explosiva. A primeira explosão, desencadeou uma reação em cadeia de explosões secundárias que rapidamente se espalharam pelo edifício de embalagem, criando uma bola de fogo visível a quilômetros de distância, como relataram os moradores de Port Wentworth. A força das explosões lançou chamas e destroços, destruindo estruturas e bloqueando rotas de evacuação.
A Propagação do Incêndio
A poeira de açúcar altamente combustível,se acumulava em torno dos equipamentos e em grande volume nos pisos da fábrica. Em alguns locais o acúmulo era tanto que chegava até a altura dos joelhos. Essa quantidade de material explosivo serviu de combustível para as explosões posteriores e o incêndio. A cada nova explosão, o pó de açúcar suspenso no ar alimentava as chamas, tornando impossível para muitos trabalhadores escaparem. As investigações foram conduzidas pela U.S. Chemical Safety and Hazard Investigation Board – CSB que revelou que toda a poeira gerada pela movimentação do açúcar na esteira era dispersada com a ajuda de jatos de ar, o que tornava a nuvem de poeira em suspensão cada vez maior. O relatório da CSB afirmou que a indústria do açúcar estava familiarizada com os perigos de explosões de poeira desde pelo menos 1925. Correspondências internas datadas de 1950 mostraram que os gerentes da refinaria de Port Wentworth estavam seriamente preocupados com a possibilidade de uma explosão de poeira de açúcar que poderia “viajar de uma área para outra, destruindo grandes seções de uma planta”. Eventos anteriores incluíram uma explosão em 1998 na planta da Imperial em Sugar Land, Texas; uma explosão na planta da Domino Sugar em Baltimore em novembro de 2007; e duas explosões de poeira de açúcar na década de 1960 que mataram um total de dez trabalhadores. A própria instalação de Port Wentworth periodicamente experimentou incêndios ao longo dos anos. Mas nenhum resultou em uma explosão de poeira de açúcar que se propagasse pela planta. No entanto, mesmo com todos esses erros passados, a gestão da empresa não deu a devida atenção que a operação do processo exigia.
O Impacto na Comunidade
A tragédia e suas consequências afetaram profundamente a comunidade, em parte porque aconteceu em uma refinaria que havia sido um importante empregador local desde 1917. A cidade sofreu uma crise econômica após o acidente, impactando a comunidade local. Muitos negócios, que dependiam dos trabalhadores e da atividade econômica gerada pela refinaria, perderam uma parte significativa de sua clientela. O fechamento temporário da fábrica e a perda de empregos criaram um efeito dominó, resultando na diminuição da renda disponível e na redução do consumo local. Como consequência, várias lojas, restaurantes e outros estabelecimentos enfrentaram dificuldades financeiras, levando alguns a fechar suas portas definitivamente.
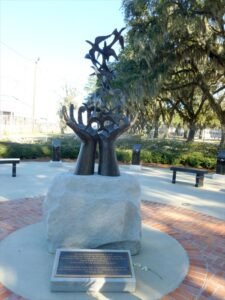
Memorial em homenagem às vítimas do acidente em Legacy Park Memorial
O Que Poderia Ter Sido Feito
A tragédia poderia ter sido evitada com algumas ações simples. Primeiro, se tivessem instalado sistemas eficientes de coleta de pó e ventilação nas áreas onde o pó de açúcar era gerado, isso teria reduzido muito a chance de uma explosão. Segundo, um programa rigoroso de manutenção e limpeza para remover o açúcar acumulado nas superfícies e nos equipamentos teria diminuído os riscos. Além disso, se tivessem realizado treinamentos regulares sobre os perigos do pó de açúcar e feito simulações de evacuação, os trabalhadores estariam mais preparados para responder a emergências.
E aqui entra uma questão importante: a implementação de tecnologia como a de sensores industriais. A evolução desses sensores remonta à década de 1950, quando começaram a ser desenvolvidos. Desde então, eles se tornaram componentes vitais para a automação industrial. Ao longo dos anos, os sensores provaram ser indispensáveis para trazer inteligência aos processos automatizados. Aplicados em larga escala em indústrias ao redor do mundo por mais de seis décadas, esses dispositivos desempenham diversas funções essenciais que contribuem para um gerenciamento inteligente das empresas. Em essência, os sensores monitoram e detectam tudo o que acontece nas linhas de produção, tornando os processos industriais mais eficientes e seguros.
No Brasil, temos a norma ABNT NBR 13862, que estabelece requisitos de segurança para o projeto de transportadores de correia. Essa norma inclui diretrizes sobre a instalação de dispositivos de segurança e monitoramento, visando evitar acidentes em operações industriais e garantir a segurança na manipulação de correias transportadoras.
No entanto, mesmo com essas tecnologias disponíveis desde 1950, a gestão da Imperial Sugar não optou por utilizá-las. Se tivessem implementado sensores para monitorar as máquinas e detectar problemas antes que se tornassem críticos, poderiam ter evitado a formação de condições perigosas. É um exemplo claro de como a falta de investimento em tecnologia e prevenção pode levar a consequências desastrosas. Foram muitos erros que poderiam ter sido evitados com medidas preventivas básicas e o uso de tecnologia avançada já disponível há décadas.
Lições Aprendidas
As lições que podemos aprender com os erros da Imperial Sugar são claras. Este incidente ressalta que a familiaridade com os riscos e a existência de registros de incidentes passados não são suficientes. A ação proativa e a implementação de medidas de segurança rigorosas e inteligentes são peças-chave para garantir uma planta segura. É fundamental que as empresas mantenham abordagens de segurança padrão, mas não podem se limitar a isso; é necessário adotar perspectivas modernas e tecnologias avançadas para evitar acidentes. A segurança no local de trabalho e seus processos deve ser uma prioridade constante, e a integração de novas tecnologias pode fazer uma grande diferença na prevenção de desastres.
Adotar uma abordagem de indústria inteligente, investindo em sensores, automação e monitoramento de velocidades, temperatura, desalinhamentos e o próprio monitoramento da poeira em si em tempo real, não só aumenta a eficiência dos processos, mas também previne acidentes. O investimento em tecnologia pode poupar as empresas de futuros aborrecimentos, evitando perdas humanas, financeiras e de reputação. Portanto, apostar na inovação e na tecnologia não é apenas uma questão de modernização, mas uma necessidade estratégica para a sustentabilidade e segurança das operações industriais.
Acima de tudo, o incidente na imperial sugar nos deixa um alerta: Afinal, quem ignora os erros do passado está fadado a cometê-los no futuro.
Recent News
Music News
-
Carga acumulada, risco elevado: entendendo as descargas eletrostáticas
27 de março de 2025 -
Kst: O número que pode explodir seu negócio (Literalmente!)
16 de março de 2025 -
Gás + Poeira = Perigo: Entenda os Riscos das Misturas Híbridas
27 de fevereiro de 2025
Sobre nós
Blog da empresa Grunn do Brasil, com matérias que exemplificarão sobre processos e aplicações das soluções oferecidas pela empresa, bem como casos de sucessos.
Acesse nosso website: https://grunn.com.br/
Categorias
- Artigos (51)
- Casos de sucesso (22)
- Guias de aplicações (2)
- Lições Explosivas (5)