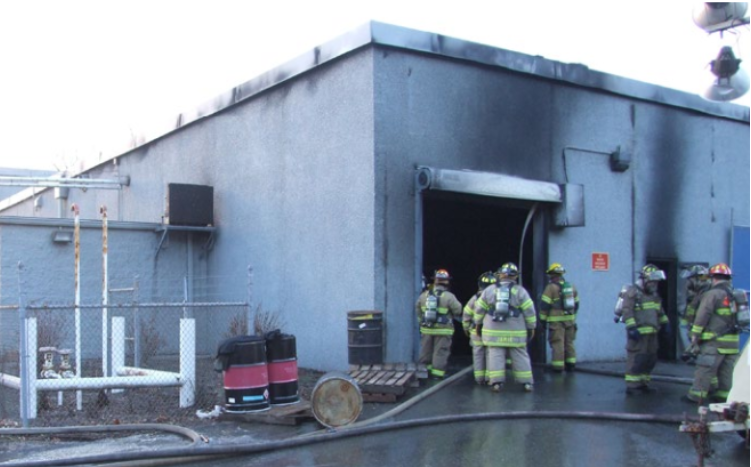
Lições explosivas | Explosão na AL Solutions: O Risco Letal da Poeira Metálica
Em 9 de dezembro de 2010, uma explosão catastrófica abalou as estruturas da AL Solutions em New Cumberland, Estados Unidos, marcando tragicamente a comunidade e a indústria de processamento de metais. A tragédia, que resultou na perda de três vidas e deixou um trabalhador gravemente ferido, devastou a instalação de processamento de metais e forçou seu fechamento permanentemente. Isso foi resultado de uma série de falhas operacionais e de segurança que poderiam ter sido evitadas com o uso adequado de tecnologias de prevenção.
Cronologia do Desastre
A AL Solutions, em New Cumberland, era uma fábrica que pulsava com o coração pesado dos metais — titânio e zircônio —, preciosos por sua resistência e perigosos por sua propensão a inflamar. Essas substâncias eram moídas e misturadas, criando um pó metálico que era prensado em discos densos chamados compactos. À medida que os metais eram desintegrados durante a moagem, o risco de um incêndio ou explosão de pó metálico aumentava na proporção em que as partículas metálicas diminuíam de tamanho.
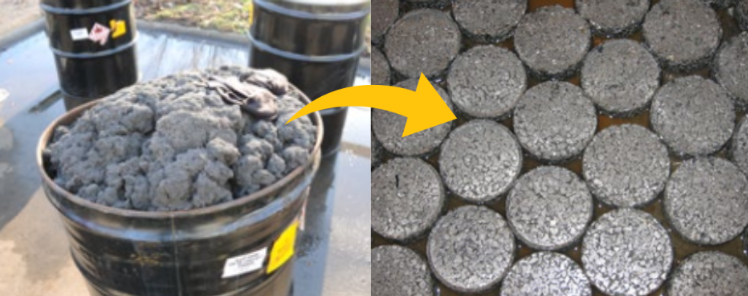
Matéria-Prima de titânio e discos compactados após o processo.
O incidente ocorreu logo após o retorno dos operários do intervalo para almoço. Durante as operações rotineiras, uma falha mecânica em um misturador de zircônio desencadeou uma faísca. No ambiente saturado de poeira metálica uma faísca foi suficiente para iniciar o desastre. Cerca das 13:20, um dos trabalhadores da fábrica próximo a uma porta entreaberta ouviu um som estrondoso, descrito como uma “falha metálica”, seguido por um ruído similar ao de acender uma churrasqueira a gás e, então, um forte estrondo. Quase simultaneamente, o supervisor de turno na sala de moagem foi surpreendido por um barulho alto e avistou um brilho laranja emanando da sala de mistura e prensa. Um segundo trabalhador, na sala hidráulica adjacente, testemunhou uma explosão na sala ao lado e viu uma bola de fogo avançar rapidamente em sua direção, queimando sua cabeça, pescoço, braços e mão enquanto ele fugia do edifício. Um terceiro trabalhador, que estava no banheiro, ouviu um ruído intenso, sentiu um vento forte e notou chamas laranjas no teto.
Um bombeiro voluntário das proximidades ouviu a explosão e rapidamente se dirigiu para o local do acidente. Os Bombeiros Voluntários de New Cumberland chegaram minutos depois. Por volta das 14h30, um helicóptero transportou as vítimas feridas para um hospital. Quando os bombeiros chegaram, encontraram o sistema de sprinklers já ativado devido às altas temperaturas. Eles tentaram acessar o prédio pelo escritório, mas o fogo intenso impediu a entrada deles. Ao penetrarem na área da explosão inicial, descobriram dois operadores mortos em suas posições de trabalho, conforme indicado nos registros da fábrica.
Os dois operadores na sala de mistura e prensa morreram no local do acidente, e o operador da prensa de zircônio faleceu três dias depois devido a graves queimaduras. O incêndio e a explosão resultaram em danos estruturais menores, como em portas, paredes e janelas, e danos térmicos mais severos em toda a área de produção. A explosão também danificou significativamente o elevador, o misturador e o transportador de alimentação da prensa, além de arremessar papéis, mesas e armários inteiros para o estacionamento externo, evidenciando a força da explosão.
Falhas Identificadas e Lições Ignoradas
Durante a investigação conduzida pelo U.S. Chemical Safety and Hazard Investigation Board (CSB), muitos detalhes vieram à tona através dos relatos recolhidos.
Os funcionários da AL Solutions notaram problemas mecânicos com o misturador nos dias anteriores à explosão. Pás do misturador estavam batendo na parede lateral do misturador e marcando a carcaça. Para resolver esses problemas, o pessoal de manutenção ajustou as lâminas do misturador para aumentar o espaço entre a parede do misturador, mas essa ação não resolveu permanentemente o problema com o contato metal-metal. Quando o problema retornou, o pessoal de manutenção decidiu substituir partes do misturador em um novo esforço para resolver o problema. Enquanto os operadores estavam desmontando o misturador, eles descobriram um grande sulco cortado no eixo e uma rachadura de 8 a 12 polegadas na parede lateral do misturador, provavelmente causada pelas pás do misturador raspando a parede lateral. O trabalhador de manutenção soldou essa rachadura, e os operadores continuaram a usar o misturador.
Na manhã do incidente, um operador solicitou que a manutenção substituísse uma pá desgastada no misturador. Um funcionário da manutenção pegou uma pá de um misturador antigo e a fixou no misturador no prédio de produção cerca de duas horas antes do incidente. Toda a manutenção realizada no misturador abordou apenas temporariamente os problemas causados pelo contato metal-metal, como o desgaste nas paredes laterais e pás desgastadas. A AL Solutions não reparou ou substituiu o misturador para evitar expor poeiras metálicas combustíveis a faíscas ou calor produzidos pelo impacto mecânico das pás. Tudo era uma grande “gambiarra” feita pelos próprios operadores para tentar sanar o problema.
Quase todos os trabalhadores, com exceção dos mais novos, relataram ter testemunhado incêndios menores no prédio de produção em várias ocasiões antes do incidente fatal. Esses relatos destacaram uma cultura de segurança falha na planta, onde incidentes menores eram frequentemente ignorados ou minimizados.
Os trabalhadores descreveram uma resposta habitualmente inadequada aos riscos conhecidos de poeira metálica. As práticas de limpeza, embora regulares, eram insuficientes para controlar a acumulação de poeira. Além disso, falhas recorrentes em equipamentos como o misturador de zircônio eram frequentemente corrigidas apenas com soluções temporárias, que falhavam em abordar a raiz do problema – o design inadequado e a manutenção insuficiente que poderiam prevenir a geração de faíscas.
Consequências e Reflexões Pós-Investigação
Os investigadores do CSB aprenderam por meio de entrevistas que os funcionários da AL Solutions estavam geralmente cientes de que o pó metálico era combustível e que uma faísca no metal poderia causar um incêndio. Em 2007, a AL Solutions contratou um laboratório para conduzir testes em amostras de sucata de zircônio e titânio. Os testes indicaram que esses componentes possuíam uma taxa de queima alta o suficiente para serem considerados “inflamáveis”.
O manual de segurança da AL Solutions listava vários requisitos para o armazenamento e manuseio seguros de ambas as substâncias No entanto, o CSB descobriu que a gerência não aplicava esses requisitos. A empresa não cumpria as práticas recomendadas de higiene industrial para o manuseio de poeiras metálicas, ignorando orientações para o uso de respiradores de alta eficiência, conforme recomendado nas Ficha de dados de segurança de materiais. Em situações de incêndio, as diretrizes de segurança da empresa instruíam os operadores a evacuar o local, notificar a gerência e contatar o corpo de bombeiros. Embora o plano de emergência contemplasse o uso de extintores de incêndio em fogos de metal, a fábrica não possuía extintores de Classe D, específicos para incêndios de metais.
A investigação da CSB também revelou que a AL Solutions não implementou controles de engenharia mais robustos que poderiam ter mitigado o risco de explosão. A falta de um sistema adequado de coleta de poeira e de uma ventilação eficaz contribuiu significativamente para o acidente. Este descaso com as medidas de segurança adequadas, combinado com a ineficácia das práticas de manuseio e armazenamento de materiais inflamáveis, demonstrou uma falha crítica na gestão de segurança da planta.
Especialistas em segurança industrial argumentam que a tragédia poderia ter sido evitada com o uso adequado de tecnologias e práticas de prevenção. Sistemas de detecção de poeira e ventilação adequada são essenciais para manter a concentração de poeira abaixo dos níveis críticos. Equipamentos elétricos e mecânicos devem ser projetados para minimizar o risco de faíscas. Além disso, a NFPA 484, a norma para o manuseio de metais combustíveis, oferece diretrizes detalhadas que, se seguidas, podem diminuir significativamente a possibilidade de tais acidentes.
Um Chamado para a Segurança Hoje
O caso da AL Solutions sublinha a importância crítica de uma vigilância constante e a aplicação rigorosa das normas de segurança. É uma chamada à ação para todas as partes envolvidas na indústria metalúrgica e regulatória para revisar e fortalecer as estratégias de segurança. A adoção e a execução de normas não devem ser vistas apenas como uma obrigação regulatória, mas como um imperativo ético para proteger vidas e propriedades. Implementar estas soluções não apenas cumpre com os regulamentos, mas também demonstra um compromisso com a ética e a proteção da vida humana no local de trabalho. A revisão regular das práticas de segurança e a atualização tecnológica são fundamentais para responder aos desafios emergentes e garantir um ambiente de trabalho seguro e produtivo.
Na era da Indústria 4.0, a integração de sensores e automação transforma as fábricas em ambientes inteligentes e conectados, essenciais para a segurança das operações industriais. Adotar uma abordagem de indústria inteligente, investindo em sensores para monitoramento em tempo real de velocidades, temperatura, desalinhamentos e, crucialmente,o monitoramento da poeira, não só eleva a eficiência dos processos mas também previne acidentes. O uso estratégico desses sensores permite coletar dados vitais sobre os processos industriais, que são transmitidos para sistemas de controle e análise.
Esses dados são fundamentais para monitorar o desempenho, identificar padrões, prever falhas e otimizar a produção. Portanto, investir em tecnologia é crucial não apenas para a modernização, mas também como uma necessidade estratégica para evitar perdas humanas, financeiras e de reputação, consolidando a segurança e a eficácia operacional no ambiente industrial.
Conclusão
A explosão em New Cumberland não é apenas uma história de perda e destruição; é um sinal de alerta para a indústria sobre a importância da prevenção ativa e do respeito pelas práticas de segurança recomendadas. A segurança no local de trabalho é um direito fundamental e uma responsabilidade compartilhada, crucial para proteger vidas e manter a integridade dos trabalhadores em todas as instalações industriais.
Recent News
Music News
-
Kst: O número que pode explodir seu negócio (Literalmente!)
16 de março de 2025 -
Gás + Poeira = Perigo: Entenda os Riscos das Misturas Híbridas
27 de fevereiro de 2025 -
Protegido ou apenas iludido? O erro na escolha de equipamentos Ex-d
17 de fevereiro de 2025
Sobre nós
Blog da empresa Grunn do Brasil, com matérias que exemplificarão sobre processos e aplicações das soluções oferecidas pela empresa, bem como casos de sucessos.
Acesse nosso website: https://grunn.com.br/
Categorias
- Artigos (51)
- Casos de sucesso (22)
- Guias de aplicações (2)
- Lições Explosivas (4)